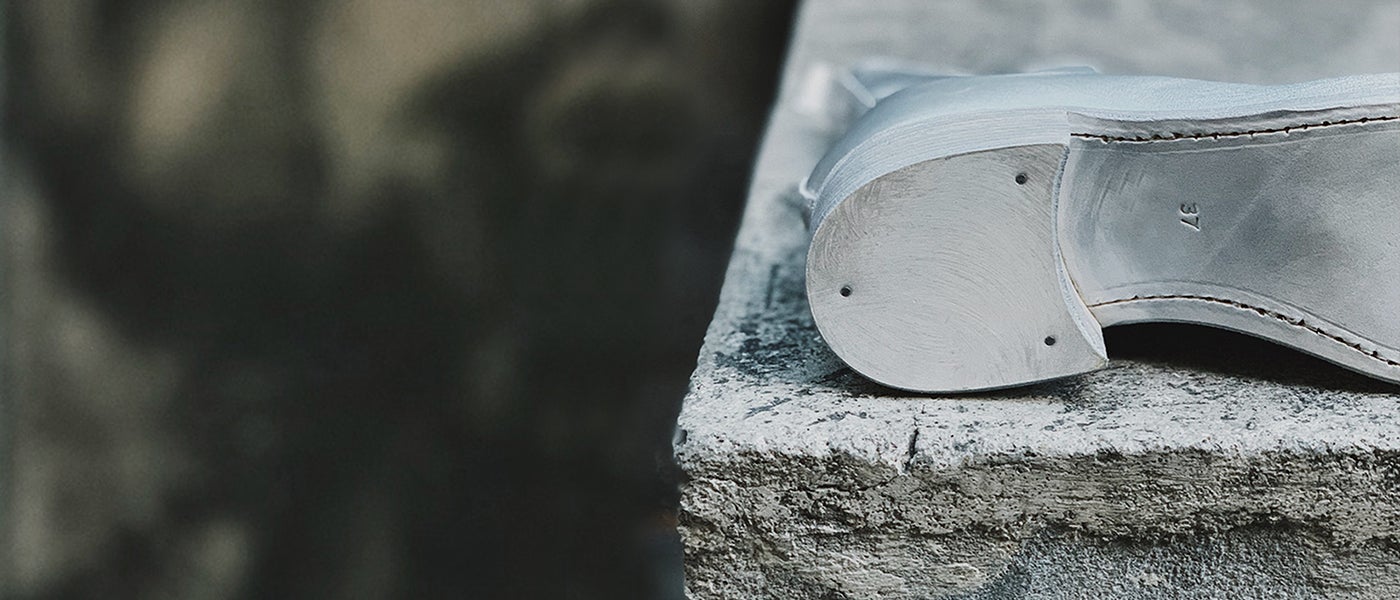
Why Buy Guidi Shoes?
Posted:
By melding centuries of artisanal tradition with a modern approach and aesthetic, Italian shoemaker Guidi certainly has amassed a cult-like international following and we've been discovering why. Tucked away in a small picturesque Tuscan town, Pescia, famous for its leather-working expertise, Guidi is a leather tannery that has been making its own shoes since 2004. In the years since the company introduced its washed, soft-looking footwear & accessories it has become a staple for well-heeled cognoscenti. To the casual eye, Guidi shoes look well-worn even when they've just left the factory floor. But this lived-in appearance is crucial to the brand's appeal.
A family-run business since 1896, and currently helmed by Ruggero Guidi, the tannery has supplied leather to some of the biggest fashion houses such as Prada, Maison Margiela & Rick Owens. Affectionately referred to as “Mr. Guidi” by all, he had long collected old workers' shoes and hiking boots. Fascinated by the historical aspect of the shoemaking process, the craftsmanship and the handmade nature, he decided to re-create the shoes. Showing the results of his experimentations around 2003 to Alessia Righi Amante, who at the time had just quit working for the cult label 'Carpe Diem' and was one of Guidi’s clients. Alessia was running a small showroom in Paris and agreed to help him sell his designs. “I liked the shoes, but they looked too new, like something people would wear to church on Sunday.” Inspired by the designs of Carpe Diem which were all about distressing, washing & doing whatever to make them look worn-in, she advised him to throw the shoes in one of the tanning drums, filled with water. The shoes reappeared charmingly distressed, although damaged in places. Nevertheless, luxury boutiques insisted on stocking them and gave birth to another idea for Amante, to dye the shoes in the drums instead of just washing them. By 2007 she was onboard to take care of sales full-time at a dedicated showroom in Paris.
The secret to the Guidi aesthetic is a method known as “object-dyeing” making the shoes both look and feel supple as well as rendering the entire shoe the same colour. A subtle yet important distinction, most shoes have a colour mismatch between the upper & the sole due to them being made at different facilities before the shoe is put together & the leather has already been dyed. By contrast, at the assembly stage, all Guidi shoes are either the natural brown of oil-tanned leather or the lighter, off-white tone of vegetable-tanned leather. Each pair is dyed after assembly as a fully formed object. This process allows the company to work on an unprecedented array of colours without losing its aesthetic signature.
The whole shoemaking process is hyper-local, each pair of footwear starts out in the company’s main facility, where the raw hides go through the tanning process in vast spinning drums. The hides are transported to the footwear factory 10 minutes away, assembled and returned to the tannery to be dyed. Guidi doesn’t own its footwear-making factory but is the only client of the factory owned by Paoli Rugiati. Like many Italian businesses, it’s been in the family for generations and his father was friends with Mr. Guidi’s father. “These kinds of traditional, regular shoes are hard to make in Italy now because of competition.. all the low- and medium-level factories in Italy have closed and we’ve lost many jobs. So now we concentrate on making high-end products.” Rugiati performs the most intricate step in the shoemaking process, cutting the shoe uppers by hand, he started learning the shoemaking process from his father when he was 15 years old. “Cutting is my favorite part of the process… you really have to know how each type of leather behaves.” Constructing a pair of Guidi’s front zip boots from the casts takes around about two hours, passing through the hands of around about a dozen artisans, slowly transforming two-dimensional pieces of leather into a boot.
Guidi uses a Goodyear welt, a method by which the shoe upper is joined to the sole via an additional strip of material (the welt) using heat-activated glue and industrial-strength stitching. A cavity between the insole and outsole is filled with cork, waterproofing the sole. When properly cared for, the shoes can last for decades, and the process of stitching the sole to the welt rather than directly into the upper makes Goodyear-welted soles easier to replace. Another subtle but important detail that gives a Guidi shoe its particular look is the stacked leather heel. The heel is made of thick pieces of leather stacked together and then glued and nailed through. To cut corners, many shoemakers have done away with this traditional process, or use plastic or pressed leather scraps instead of real leather. Once the boots are assembled, the last step is to carefully sand down the raw outer edges of the sole and strip away any glue spots.
The freshly constructed shoes come back to the tannery and are dyed in a machine that looks like a huge, stripped-out washing machine. The dyeing is done by a single operator, Mr. Giacomo, who also mixes all the colours, tests them, and comes up with new ones. Only one colour can be applied at a time for up to 25 pairs. The process takes approximately 40 minutes. If the dye doesn’t take correctly, the boots go back for another 40-minute session. The process is a mixture of art and science. “Black is the hardest color to get right,” Mr. Giacomo says. “And different leather types take the dye differently.” After the shoes are dyed, they go to an adjacent building for drying, quality control, packing, and shipping. On average, it takes a week for a shoe to air-dry. They’re then moved to another station for examination and packing according to store orders.
For Guidi, shoemaking started out as a passion project, but it now surpasses the tannery part of the business. A company that has stayed true to its aesthetic principles, Guidi refuses to bow to trends. A significant part of Guidi’s growth is due to its popularity in China. “Several years ago, Chinese movie stars and musicians started wearing Guidi, as they were becoming more conscious of the fashion avant-garde,” says Lu Han, owner of Atelier New York, a major stockist. Han points out other factors that have contributed to Guidi’s popularity, such as the brand’s use of horse leather, the unconventional look of its shoes, and comfort. Guidi’s relative scarcity has spawned an entire industry of fake products. Each pair of authentic Guidi shoes now comes with a QR code that confirms the product’s origins via authentication. Success is a double-edged sword for the brand. “I’m glad people are buying our shoes, but I hope they buy them for the right reasons,” says Righi Amante, who is concerned about the average customer treating Guidi merely as another fashion product to be consumed and discarded according to trends. “We want them to know about the artisanal process, about the craftsmanship.”
Guidi’s dedication to these traditional business and manufacturing processes has made traditional manufacturing modern, carving out a niche for people who care about how things are made. Guidi consumers understand the aesthetic premise and underlying quality each shoe represents. A Guidi shoe is made using the best available materials and techniques. Luxury by definition is an indulgence, however, consumption of luxury fast fashion brands is in no way comparable to slow-made fashion, hand-stitched by artisans. Guidi shoes invite its wearer to continue adding to the story with further wear, their signature. A shoe that could only be made by an artisan, it doesn’t scream luxury despite its high price point, instead quietly presenting as an understatement bordering on disdain - and that’s exactly their appeal.
From left to right Chunky Sole Leather Boots W Front Zip - Black, White, Black Suede
Discover the full range of Guidi Shoes available at the Shelter here.